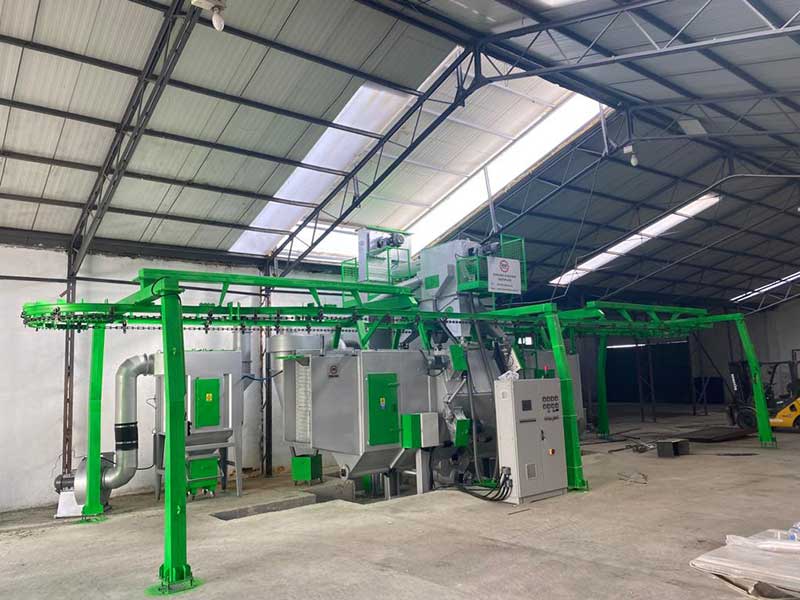
Continuous hanging sandblasting machines are advanced equipment designed to meet the needs of continuous and high-volume sandblasting in industrial surface treatment processes. These machines enable continuous sandblasting, especially of large, heavy or complex geometry parts on mass production lines, significantly increasing production efficiency.
Working Principle:
Continuous hang shot blasting machines are based on a principle in which parts are continuously transported to the blasting cabinet via a conveyor system or rail system and brought into contact with abrasive materials, which are sprayed at high speed by rotating hangers or hooks by rotating hangers or hooks. This process continues uninterrupted from the entry and exit of the parts into the blasting cabinet, thus ensuring a continuous production flow.
Basic Components of Continuous Hanging Sandblasting Machines:
- Conveyor or Rail System: It is the mechanism that allows the parts to be transported to the sandblasting cabinet continuously.
- Suspension or Hook System: It is the mechanism that allows the parts to be rotated and positioned in the cabin.
- Sandblasting Cabinet: It is the closed area where abrasive materials are sprayed and parts are sandblasted.
- Abrasive Blasting System: It consists of turbines or nozzles that spray abrasive materials onto parts at high speed.
- Abrasive Recovery System: It is the system that ensures that the abrasive materials used are collected and made ready for reuse.
- Dust Collection System: It is the system that ensures that the dust and other particles formed during the sandblasting process are separated from the air and the environmental effects are minimized.
- Control System: It is an electronic or mechanical control unit that allows the adjustment and monitoring of the operating parameters (rotation speed, spray pressure, etc.) of the machine.
Operation Steps:
- Part Loading: The parts to be processed are loaded on the conveyor or rail system.
- Transport into the Cabin: The conveyor or rail system transports the parts into the sandblasting cabinet.
- Sandblasting Process: The abrasive blasting system sprays abrasive materials onto parts at high speed. The hanger or hook system rotates the parts, ensuring that all sides are sandblasted evenly.
- Abrasive Recovery: The abrasive materials used fall to the bottom of the cabinet and are collected by the recovery system and made ready for reuse.
- Dust Collection: The dust and particles generated during the sandblasting process are filtered by the dust collection system.
- Unloading: After the sandblasting process is completed, the conveyor or rail system carries the parts out of the cabin.
Uses:
- Automotive Industry: Mass production of large automotive parts such as chassis parts, rims, engine blocks.
- Shipbuilding: Cleaning and surface preparation of large ship parts such as ship hulls, propeller parts.
- Railway Industry: Cleaning of large railway equipment such as train cars, track tracks, wheelsets.
- Structural Steel: Mass production of steel constructions, bridge parts, large pipes.
- Aerospace Industry: Cleaning large aviation parts such as airframe parts, landing gear, etc.
Advantages:
- High Production Efficiency: Continuous flow and automation improve production speed and efficiency.
- Low Labor Costs: Automated systems minimize human intervention.
- Consistent Quality: Control systems provide consistent and repeatable blasting results.
- Material Saving: Integrated recovery systems optimize the use of abrasive materials.
- Machining of Large and Complex Parts: The suspension system allows easy machining of large and complex geometry parts.
Continuous hanging sandblasting machines are an important technology in industrial production processes that enables the sandblasting of large and complex parts in mass production lines with high efficiency and quality.