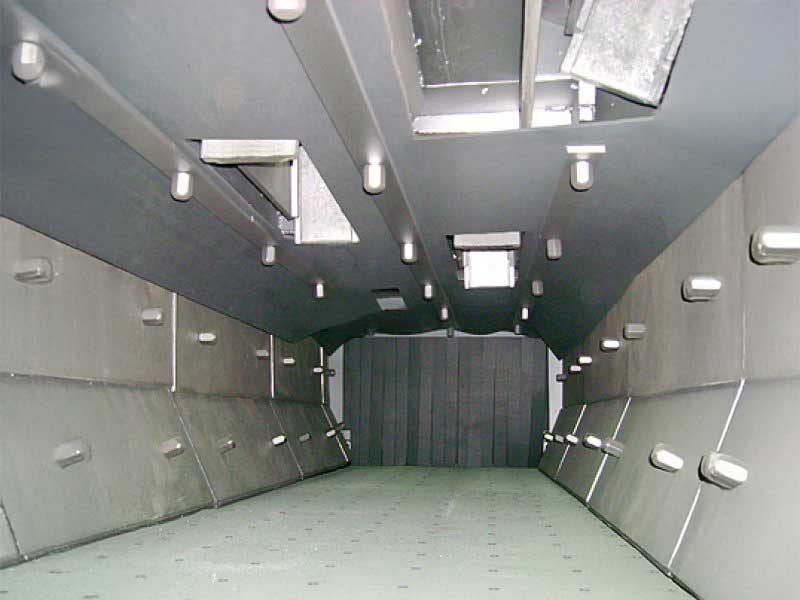
Sandblasting cabinets are closed systems designed to perform sandblasting in industrial surface treatment processes, especially in a controlled and safe environment. These cabinets are used for cleaning, roughening or surface preparation by spraying abrasive materials at high speed.
Key Components of Sandblasting Cabinets:
- Cabinet Body:
- The cabinet body, usually made of durable steel or stainless steel, prevents corrosive materials and dust from leaking out.
- Lighting System:
- Powerful and durable lighting systems are used to ensure adequate visibility inside the cabin.
- Ventilation and Dust Collection System:
- There are high-efficiency ventilation and dust collection systems to remove and filter dust and particles generated during the sandblasting process from the cabin.
- Abrasive Blasting System:
- It includes nozzles or turbines that spray abrasive materials at high speed through compressed air or mechanical turbines.
- Recovery System:
- There are recovery systems for collecting and cleaning the abrasive materials used and making them ready for reuse.
- Control Panel:
- There is a control panel where all systems in the cabin are controlled and adjusted.
- Observation Window and Gloves:
- There is a durable observation window and gloves for the operator to safely observe the process and manipulate the parts.
Types of Sandblasting Cabinets:
- Pressure Sandblasting Cabinets:
- It sprays corrosive materials using high-pressure air. Suitable for heavy duty and difficult surfaces.
- Vacuum Sandblasting Cabinets:
- It operates in a closed system and recycles corrosive materials, providing an environmentally friendly solution. Ideal for sensitive surfaces and confined spaces.
- Wet Sandblasting Cabinets:
- These are cabinets where abrasive materials are mixed with water and sprayed. It minimizes dust formation and is suitable for sensitive surfaces.
Uses:
- Metalworking:
- Cleaning of metal parts, removal of rust and paint, surface roughening.
- Automotive:
- Cleaning and preparation of engine parts, rims and other automotive components.
- Aviation:
- Cleaning of aircraft parts and surface preparation.
- Cast:
- Cleaning and deburring of casting parts.
- Restoration:
- Cleaning and refurbishment of old structures and objects.
Things to consider when choosing a sandblasting cabinet:
- Size and Shape of the Parts to be Machined:
- Cabinet dimensions and design must match the dimensions and shapes of the workpieces.
- Sandblasting Needs:
- The desired surface finish and level of cleanliness determine the type of cabinet and abrasive blasting system.
- Working Environment:
- The cabin must have ventilation and dust collection systems in accordance with the requirements of the working environment.
- Security:
- The cab must have the necessary safety measures to ensure operator safety.
Sandblasting booths are an important piece of equipment that improves efficiency, quality, and safety in industrial surface treatment processes. Choosing the right cabinet is critical to optimizing production processes and reducing costs.