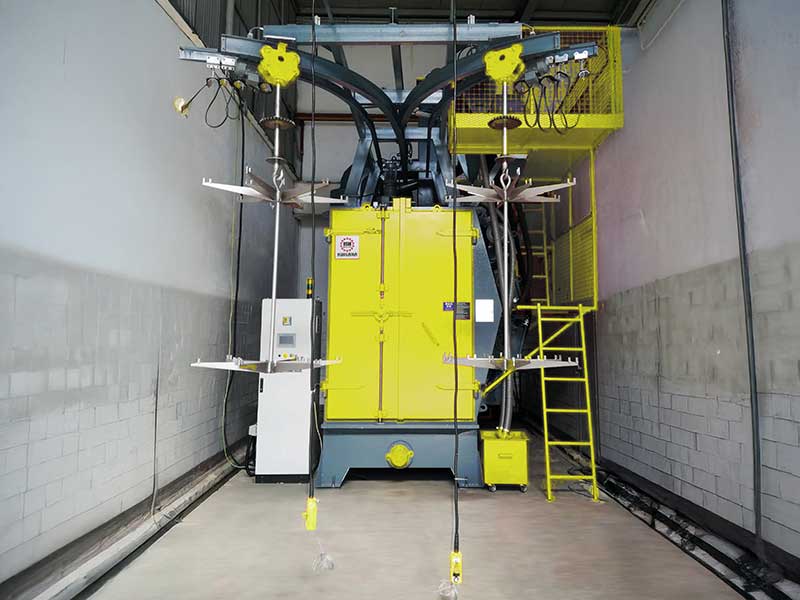
Suspended sandblasting machines are specialized equipment designed for cleaning, roughening or preparing parts with large, heavy or complex geometries in industrial surface treatment processes. These machines work on the principle that the parts are suspended from the sandblasting cabinet by means of rotating hooks or hangers and brought into contact with abrasive materials (usually steel granules or ceramic balls) that are sprayed at high speed.
Basic Components of Hanging Sandblasting Machines:
- Sandblasting Cabinet: It is the closed area where abrasive materials are sprayed and parts are sandblasted.
- Suspension or Hook System: It is the mechanism that allows the parts to be rotated and positioned in the cabin.
- Abrasive Blasting System: It consists of turbines or nozzles that spray abrasive materials onto parts at high speed.
- Abrasive Recovery System: It is the system that ensures that the abrasive materials used are collected and made ready for reuse.
- Dust Collection System: It is the system that ensures that the dust and other particles formed during the sandblasting process are separated from the air and the environmental effects are minimized.
- Control System: It is an electronic or mechanical control unit that allows the adjustment and monitoring of the operating parameters (rotation speed, spray pressure, etc.) of the machine.
Working Principle:
- Part Loading: The parts to be processed are loaded into the hanger or hook system.
- Transport into the Cabinet: The hanger or hook system transports the parts into the sandblasting cabinet.
- Sandblasting Process: The abrasive blasting system sprays abrasive materials onto parts at high speed. The hanger or hook system rotates the parts, ensuring that all sides are sandblasted evenly.
- Abrasive Recovery: The abrasive materials used fall to the bottom of the cabinet and are collected by the recovery system and made ready for reuse.
- Dust Collection: The dust and particles generated during the sandblasting process are filtered by the dust collection system.
- Parts Unloading: After the sandblasting process is complete, the hanger or hook system carries the parts out of the cab.
Advantages of Hanging Sandblasting Machines:
- Machining of Large and Heavy Parts: The suspension system allows easy machining of large and heavy parts.
- Machining of Complex Geometries: The rotating suspension system ensures that all sides of parts with complex geometries are sandblasted evenly.
- High Efficiency: The ability to sandblast multiple parts at the same time increases the production speed.
- Flexibility: Various part sizes and shapes can be machined using different hanger and hook systems.
Uses:
- Foundry Industry: Cleaning and surface preparation of large casting parts.
- Welded Fabrication Industry: Cleaning and roughening of welded structures.
- Shipbuilding: Cleaning and pre-painting preparation of ship parts.
- Railway Industry: Cleaning of train wagons and track parts.
- Aerospace Industry: Cleaning and surface preparation of aircraft parts.
What Parts Are It Used For:
- Large casting parts (engine blocks, turbine housings, etc.)
- Welded structures (steel constructions, tanks, etc.)
- Ship parts (hull plates, propellers, etc.)
- Train wagons and track parts
- Aircraft parts (wing parts, landing gear, etc.)
Hanging sandblasting machines are an indispensable tool for surface treatment of large and complex parts in industrial production processes.